Pallet & load quality
- Keith D Goodfellow (SARI)
- May 6, 2020
- 3 min read
Updated: Jan 15, 2021
Pallet and load quality are critical to safety in your warehouse. A damaged pallet is a dangerous pallet. Even an empty pallet can weigh 20-25kg so if it falls out of the racks it is lethal. Likewise if even an empty cardboard box falls off a pallet and you look up at the wrong time and it catches you in the eye it’s a rushed trip to A&E. Even a nut or bolt falling from 6 or 7 metres can be a killer. So we need to ensure that any pallet placed in the racks is suitable for those racks both in terms of type and size, is good quality and that the load is safely stacked and secure. So firstly let’s consider the pallet type and construction.
Pallets
1,200mm x 1,000mm perimeter based pallet
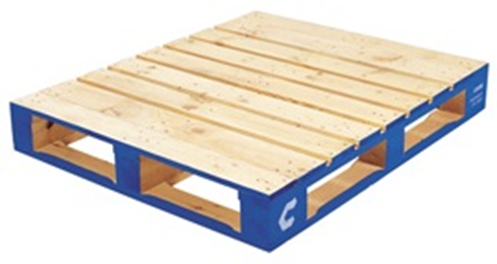
The UK type pallet characterised by the Blue Chep pallet is 1,200mm x 1,000mm perimeter-based pallet as shown in the photo above. Perimeter based means the bottom boards run on both the 1,200mm and 1,000mm dimension meaning the pallet can be stored in either orientation provided the racking frame is the correct size – this is covered in my post Pallet Positioning.
1,200mm x 800mm non perimeter based pallet

The Euro pallets is a different size and construction. It is 1,200mm x 800mm so a bit smaller then the UK pallet. If you look at the photo above and compare it to the UK pallet you will see that it doesn’t have boards running on the shorter 800mm dimension meaning it must be stored 1,200mm into the racks since doesn’t have sufficient strength to stored on the 800mm dimension without additional support such as decking or pallet bars.
And so to pallet quality. You must ensure that the pallet is sound with no obvious damage or defects. Broken, loose, or missing boards & fixings for example would render it unsafe so drivers must be made aware of the need to check every pallet being placed in the racking. A damaged pallet is a dangerous pallet. You should also consider you procurement process. Ensure that your procurement department is aware of the need to specify a type and standard of pallet and also the load dimensions, especially the height. My experience is its usually far cheaper and more effective to have the stock delivered on the correct pallet allowing immediate put away in the racks rather than have staff constantly destacking loads because they are too tall for your pallet locations or repalletising at goods because it is an unsuitable pallet inwards taking up valuable space and time and delaying put away.
Load quality
Let's not forget load quality. All loads should be secured to the pallet with banding, stretch wrapping or other suitable means to ensure nothing becomes dislodged which also applies to part picked pallets. For those environmentally conscious people who want to eliminate the reliance on and wastage of stretch wrap and other packing materials I’ve seen elasticated strapping with Velcro fixings which seem very effective. Box flaps should be closed and there should be nothing overhanging the footprint of the pallet since anything overhanging the pallet is at risk of becoming dislodged and will also reduce the safe stacking clearances which are covered in a separate blog Pallet positioning. Tall or potentially unstable loads should be secured to the pallet with strapping or load securing straps. Where random lose items are stacked pallet cages or pallet collars can be effective.
With high level picking, part picked loads and loose boxes are inevitable. It is essential therefore that part picked loads on pallets are carefully managed with nothing overhanging the pallet. Box flaps should be closed and a procedure for stacking boxes developed.
These guidelines are applicable to everyone operating in the warehouse so all you staff should be made aware of these simple guidelines. All staff need to be the eyes and ears of safety and encouraged to flag up non-conformities as soon as possible so they can be rectified. Remember, if you don’t look you won’t see!
Kommentare